Four Axis CNC Porting
Our Highly Developed 4-Axis CNC Porting Process has Prepared Literally Thousands of Heads Over More Than a Decade
Our 4-Axis CNC process cut it's first head in 2003, and since then we've run literally thousands of head through it, producing powerful street and race bikes across the globe.
A huge amount of R&D went into this process, and many of the things described below are still in use as we now transition to 5-axis CNC as described above. Follow along as
we describe how 4-axis CNC based operations are fully integrated into head preparation.
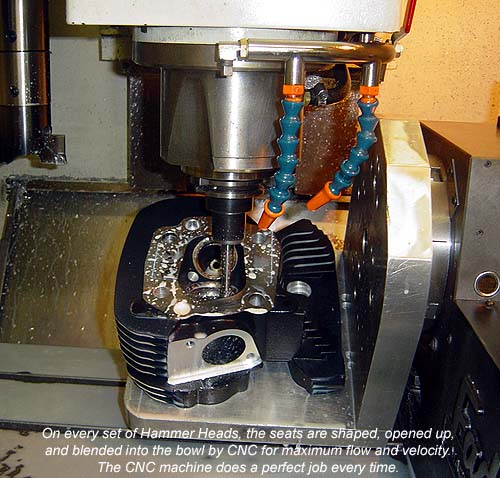
This is one of the first steps to get done to any set of heads. Once they're stripped and inspected, they're put into the 4-axis CNC machine in this position to get the seat work done.
Well, there are a lot of possibilities on this step. What size valves are the heads getting? What's the current seat i.d.? What kind of head is it? Is it a front or a rear head?
Will it need new seats?
The problem here is that there are SO many possibilities, that keeping a separate CNC machining program for every one of them would be next to impossible. You'd have thousands of
programs to choose from, and you'd have an error prone process. So here's our solution:
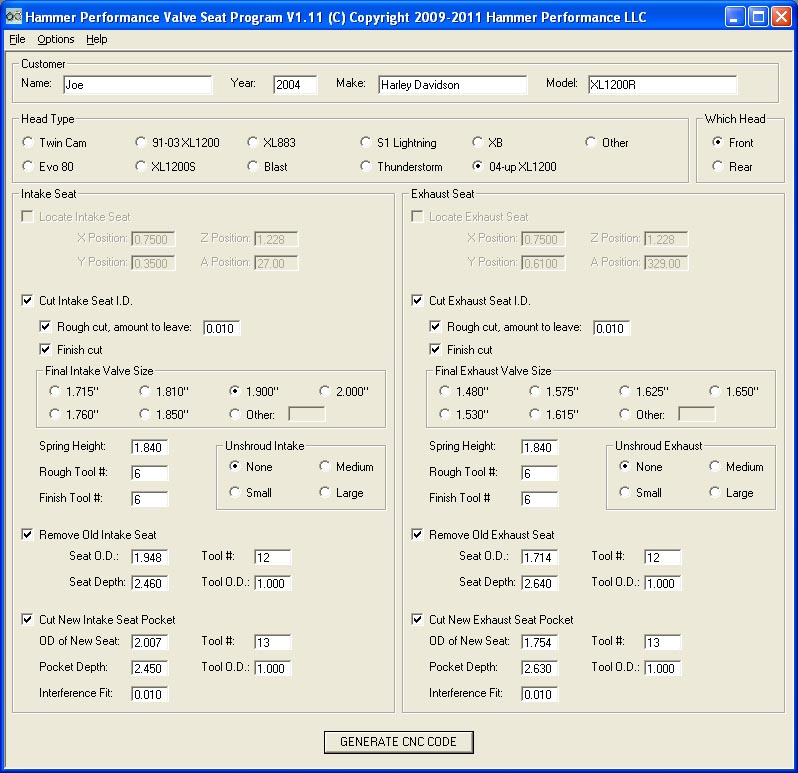
We developed this program specifically to perform all seat operations. Basically, you enter all the information, and hit the "GENERATE CNC CODE" button down at the bottom
of the screen, and the program goes off and writes the CNC program and then offers to send it to the machine. HAMMER Dan then punches a few buttons on the machine to get it ready,
and hits OK, hits the "Start" button on the machine, and off it goes.
The top line in this program takes in info about the customer, as the program keeps a log of everything done to every set of heads. Head type and which head (f or r) is chosen next.
Then on the left you have everything to be done to the intake seat and on the right is the exhaust seat. You typically start by doing a "locate" operation.
Since heads vary from one to the next, this step allows you to use an indicol to precisely locate the center of each valve. Once it's located you then set it up
to do the cuts. You can cut and shape the seat, blend and unshroud it into the chamber, remove the seat completely, and/or cut a new seat pocket whatever size you want.
When we cut the seats at this step, we intentionally leave a little material in them, because later we'll cut them again with the actual guides. You can see in the screenshot
how we've selected "Rough cut" and are leaving .010" of material. So we rough cut them in, then remove the stock guides, and move on to cutting the ports:
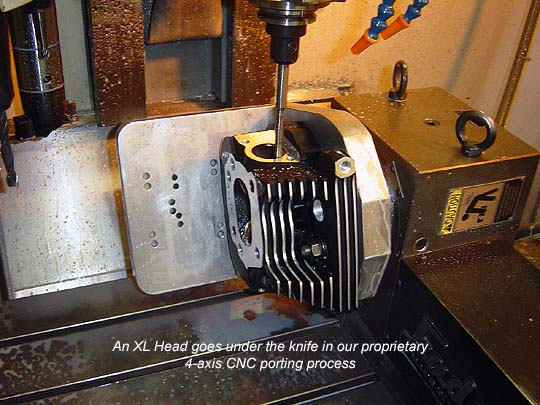
Again in 4-axis mode, the machine cuts the ports to the proper size and shape. But just like the seat operations, there's a dizzying array of possible combinations in terms
of what you want the machine to do. So naturally we created a program to sort this out:
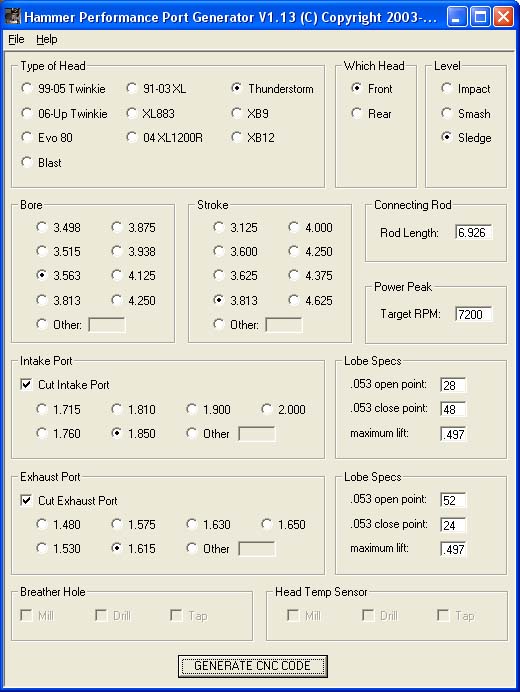
This is our main porting program. But it actually does a lot more than just let you select operations. If you choose the "Sledge" mode as shown, the program allows you to enter
application specific parameters, like the bore, stroke, rod length, target power peak rpm, and cam timing. The program then goes off and does a bunch of math to figure out the
ideal port size, and dynamically generates a CNC porting program to cut the port that size. This overcomes one of the big, big limitations of CNC porting, the ability to custom
tailor the port to the application. It's the best of both worlds, you get the accuracy and repeatability of CNC with the custom capability of hand porting. I'm not aware of any
other shop that has anything else like it.
Once that's done, HAMMER Dan does the hand blending. There's a fair bit of variation from one head to the next, and also there are some areas in the port where the CNC can't
reach well. Dan is very talented and experienced at smoothing the variations and shaping the places the CNC can't reach.
Once the ports are right, Dan presses in new guides, sizes them for proper stem clearance, runs them through the machine again to get the seats to the final size with
the final guides, and then puts the final valve job onto the seats:
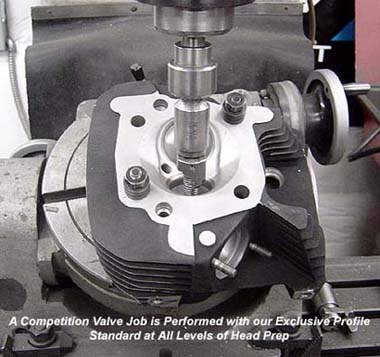
During this step he also sets the stem protrusions for the correct geometry and proper valve to valve clearance. We use specially shaped seat cutters of our design on
the seats themselves. We've found this process to work much better than using stones or other methods. The seat profiles for the two valves are very different as well,
as their functions are different. For example, the exhaust seat has a much wider 45 degree area because one of the important functions of the exhaust seat is to pull heat
away from the valve.
Any chamber work the heads need is performed as well:
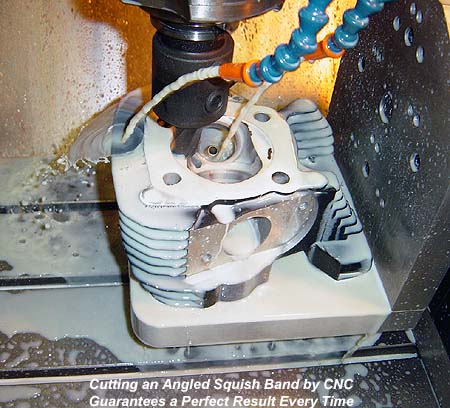
This head is getting an angled squish band in the CNC machine.
And you guessed it, we have a program for that, too:
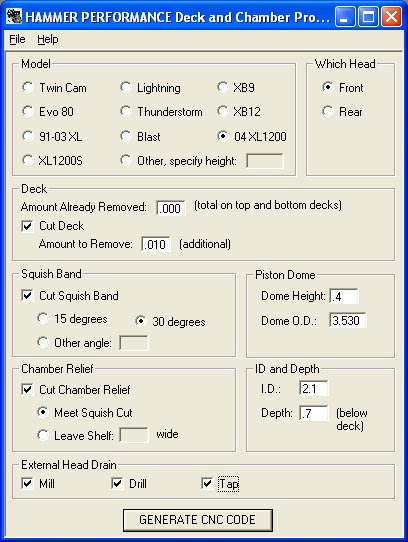
This program is also used for cutting the deck, which goes hand in hand. Note the mentions of external head drains, the programs do this for us as well.
HAMMER Dan will iterate on this step until he gets the chamber size right where he wants it, to give the customer the compression ratio he wants:
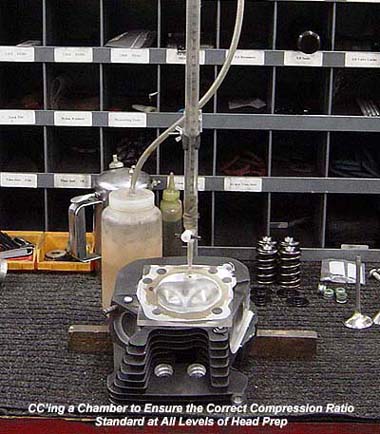
And of course, EVERY head gets flow tested before it leaves the shop:
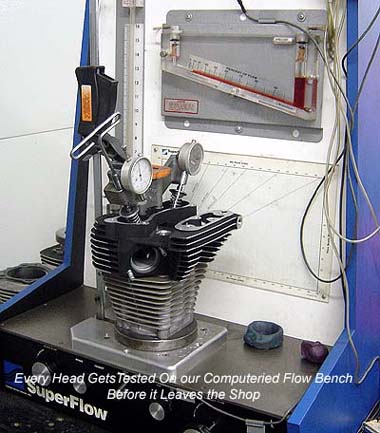
Finally, once the heads are perfect, HAMMER Dan assembles them with the finest hardware available:
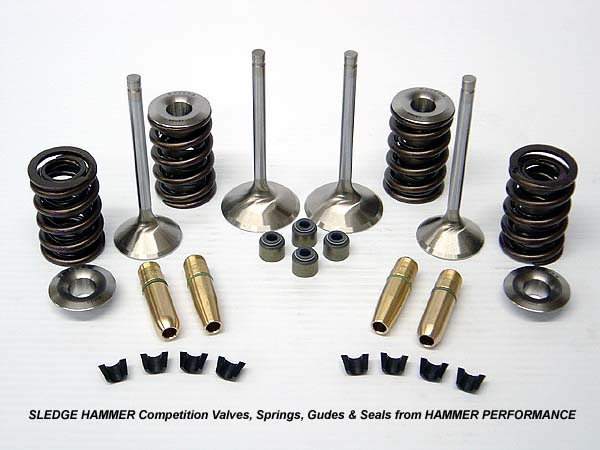
The springs are of course shimmed as needed for the proper installed height, to give the required seat pressure and travel.
And finally the heads are ready to go back to the customer:
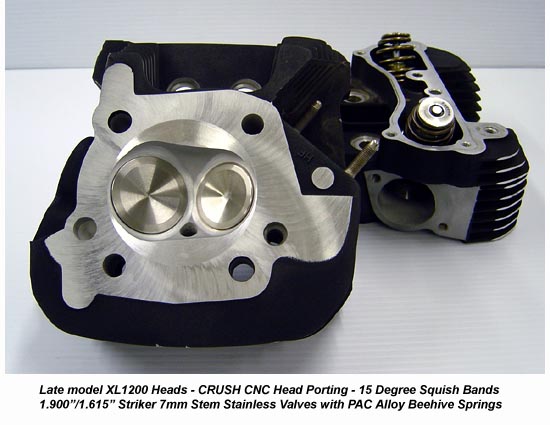
This process has served us well. We run hundreds of sets of heads through the shop every year, and we've proven time and time again to deliver a superb quality product
that performs exceptionally well. We believe the HAMMER PERFORMANCE head porting process has put more XL's in particular over 100hp than anyone out there.
If you'd like to treat your heads to this process, give us a call or shoot us a note. We look forward to helping make your project a success!
|